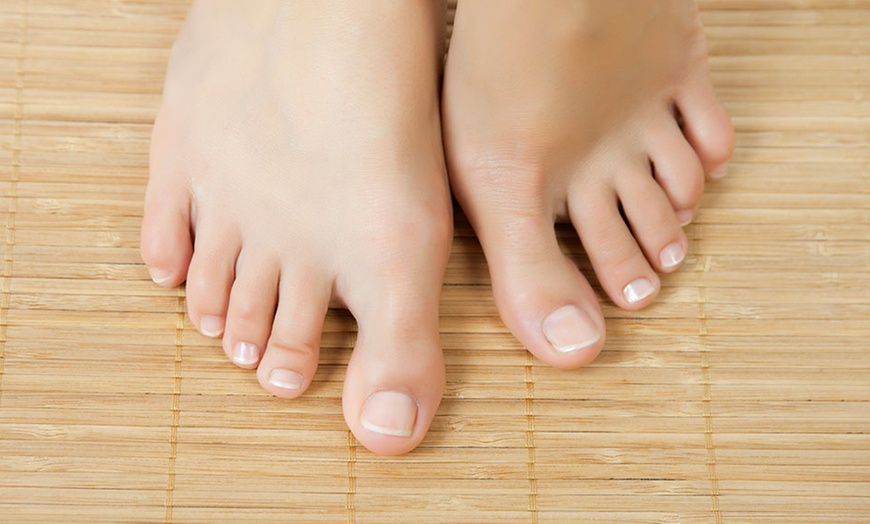
It can be difficult for rough lumber to be loaded into your car. When you visit the store, make sure you have your tape measure and hand saw. In case your board does not fit, you can purchase additional boards. It is important to ensure the board you buy has knots and checks. If they don't, it may not plane as smoothly as you had hoped. It's not worth ripping a board and starting over. It will take time and cost you money. So, it is a good idea to buy a few extra boards.
There is less waste
When cutting rough lumber, a sawmill typically turns 59% of the log volume into boards. The remainder of the log can be considered waste, including sawdust, bark, chips and chips. A less-than-perfect cut results in more waste, but it should still be less than 20%. Here's how to estimate the amount wasted wood in a board. The sawmill should reduce 18% of its volume in order to get the desired lumber thickness.
Rough lumber is not always available in standard dimensions. The dimensions of hardwood you buy from big box stores are usually known. This allows you to plan your project according to the standard size. That means the edges of rough lumber don't always line up, resulting in waste. Also, rough-cut lumber is usually of a similar width. This results in a lot more lumber being wasted. And this waste can't be used later.
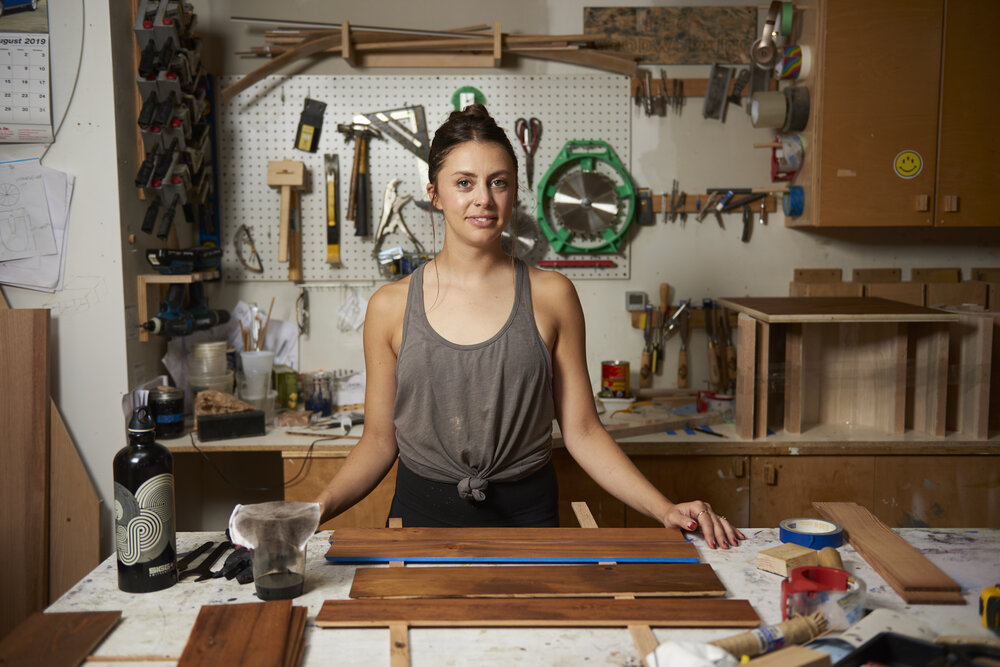
Preparation
The first step in preparing for cutting rough lumber is to measure the length of the material. Rough lumber might not arrive flat at the lumber yard. It might not have parallel faces or edges and may require multiple passes to flatten. The rule of thumb is 1/16" per pass. If your lumber has concave surfaces you should run it through the saw keeping the concave surface in place.
The rough cut lumber should generally be flattened to 1/4" before the saw cuts. After flattening the face, plane to the thickness of the finished board. Once you have measured the rough lumber's thickness, measure the finished width & length. Be aware of any imperfections and plan accordingly. Be sure to leave a minimum of one-quarter inch space on each side of the board. You can also plan your project using the available boards. Do not buy lumber that is uneven. It will be difficult to work on boards that are bowed, warped or twisted.
Cost
There are two types. Dimensional lumber and rough-sawn. Generally, home improvement stores carry finished lumber but rarely rough-sawn lumber. Lumber yards and local sawmills tend to carry both types of lumber. The only difference between these two types lies in the work involved. The cost of rough-sawn lumber is lower because it needs less processing. It is also more flexible than finished lumber in that it can be cut wider and thinner.
A lumber yard or mill will generally sell lumber at a lower price, but they are less likely to have standard lengths. You can mill your own lumber for a cheaper alternative to purchasing rough-sawn lumber. However, you will need more shop space and higher power. Milling equipment is noisy and requires training. Consider the local zoning laws if you intend to use your mill.
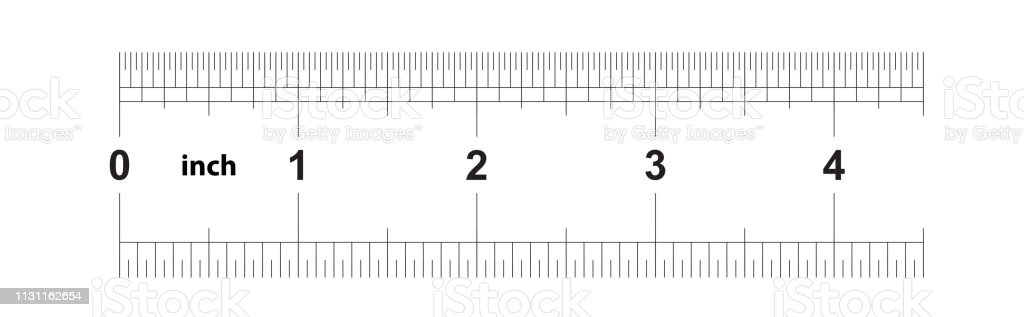
Source
There are many options available when you buy lumber. There are many sizes, shapes and finishes available. Rough sawn lumber is unfinished, unsanded lumber that has been cut into planks. This type of lumber tends to be stronger than other types because it carries extra moisture, but it is also thicker than surfaced wood. These are some of many advantages to rough sawn lumber in your woodworking projects.
The first is the availability and low cost. Rough lumber is not treated and is not usually sold at a hardware store. However, this type of lumber has its pros and cons. It's cheaper by volume but more expensive per board foot to haul. It takes longer to finish than treated wood. So, you might want to consider this option when you're deciding how much lumber to buy. If you plan on using rough sawn lumber for your project, consider purchasing a large quantity of it and a small amount for finishing.
FAQ
Can I refinish furniture that I make?
Yes! There are plenty of ways to refinish old pieces of furniture without having to pay a pro. Here are some suggestions:
Use sandpaper to remove scratches and stains. Use a clean cloth to wipe the surface.
Clear polyurethane varnish should be applied. Allow furniture to dry completely before you move it around.
Use acrylic paint to paint furniture.
Instead of using paint, stain is a better choice. The furniture will have a rich look thanks to the stain.
Use shellac wax. You can protect your wood with wax and give it shine.
Can I make a living doing this?
Yes! In fact, most woodworkers already have it. According to the U.S. Bureau of Labor Statistics' (BLS), in May 2012 the median annual wage of woodworkers was $34,000 This is higher than the $31,000 annual national average.
What tools should I start with when becoming a woodworker?
Woodworking is an art form that requires patience and practice. It takes time to master all the tools and techniques involved in woodworking.
There are many options for woodworking equipment today. Some prefer to use power tools and others prefer hand tools.
The choice is yours, but you must ensure you choose the right tool for the job. If you don't have any experience, you may consider starting with a basic set of hand tools.
You might also want to learn how a router works, which allows you to cut wood into intricate shapes. These routers can be purchased at most hardware and home improvement stores.
How do you know which type of wood you are working with?
Always check the label before purchasing wood. The label should include information about the wood species and its moisture content as well as whether or not it has been treated using preservatives.
What should a woodworker be paid per hour?
The hourly rate for a professional Woodworker will vary depending on many variables, such as experience, skill level and availability.
An average hourly rate for skilled woodworkers ranges between $20-$50.
A less skilled woodworker might charge as low as $10 per hour.
Statistics
- In 2014, there were just over 237,000 jobs for all woodworkers, with other wood product manufacturing employing 23 percent; wood kitchen cabinets and countertop manufacturing employing 21 percent. (theartcareerproject.com)
- If your lumber isn't as dry as you would like when you purchase it (over 22% in Glen Huey's opinion…probably over 10-15% in my opinion), then it's a good idea to let it acclimate to your workshop for a couple of weeks. (woodandshop.com)
- Woodworkers on the lower end of that spectrum, the bottom 10% to be exact, make roughly $24,000 a year, while the top 10% makes $108,000. (zippia.com)
- The U.S. Bureau of Labor Statistics (BLS) estimates that the number of jobs for woodworkers will decline by 4% between 2019 and 2029. (indeed.com)
External Links
How To
How to make wood joints
This tutorial will demonstrate how to join two pieces together of wood. We will use the pocket hole joint, which is drilling holes in the wood to join them. This works well if the wood is straight and smooth. You may want to consider other methods, such as dowel joining. Here are the steps
-
Drill Pocket Hole Joints. First, measure the area where you wish to place the pocket joint. Use a jigsaw or handheld drilling machine to drill 3/8 inch deep holes at the ends of each wood piece.
-
Sand Smooth. Sanding the edges of the wood will help to prevent the joint from splitting later.
-
Glue together. Apply glue on both sides of the wooden plank. Allow it to cool for at least 5 minutes before you attach the pieces.
-
Connect the pieces. After the glue has dried properly, clamp the pieces together to make sure they are flush.
-
Trim Joinery. Trim the excess wood around the joint after the glue has dried completely.
Make sure to leave enough room between the pieces so that you can turn them inside and out.