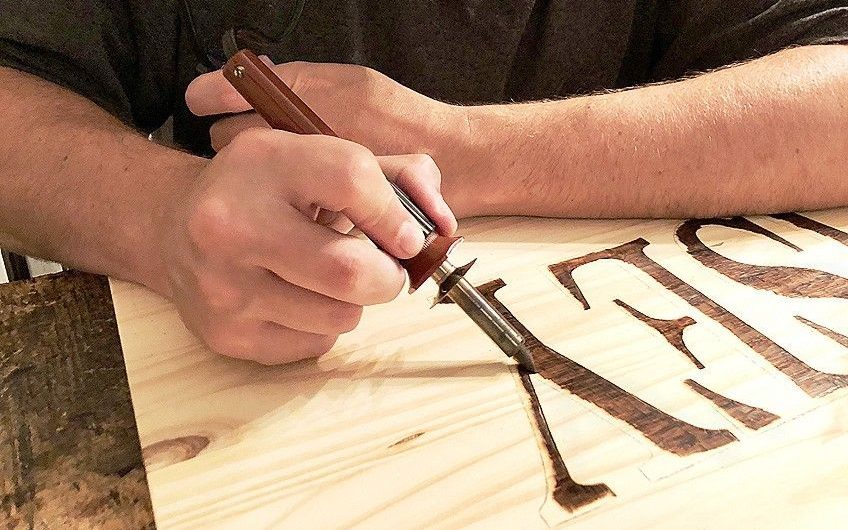
To get started with wood burning, you will need graphite paper, wire brush, and a Pyrography pen. You can use them to trace the design and add shading and more detail. You can also use a stencil to create a unique design. This will save time and help you avoid frustration. Be sure to double-check your supplies! You may not have everything you need! Continue reading to find out how you can create your wood burning design.
Untreated wood
Many types of untreated wood can be used in wood burning designs, but they are not the best. Wood is a natural source of fuel, but it can also be an irritant or toxin. Many wood species also come in a variety of different forms, some with worse health than others. In general, it's best to avoid wood with these properties. Here are some tips to help you choose the right wood for your wood burning project.
Untreated wood, which is the naturalst of all, is the best. Untreated wood can also be found at your local craft shop or hardware store. Many stores carry pre-cut pieces of wood, so you won't have to waste a ton of time measuring and cutting. Lumber yards may also be a great source of freshly cut wood, which is seasoned. However, untreated wood will be more costly.
Graphite paper
Graphite paper can be used to transfer designs to your wood burner. Simply transfer your design to graphite paper, then attach it with tape. Once you have it securely in place, you can start burning! Be sure to use light- to medium-pressure and to follow the design lines exactly. You will be amazed at what you get when you are done burning!
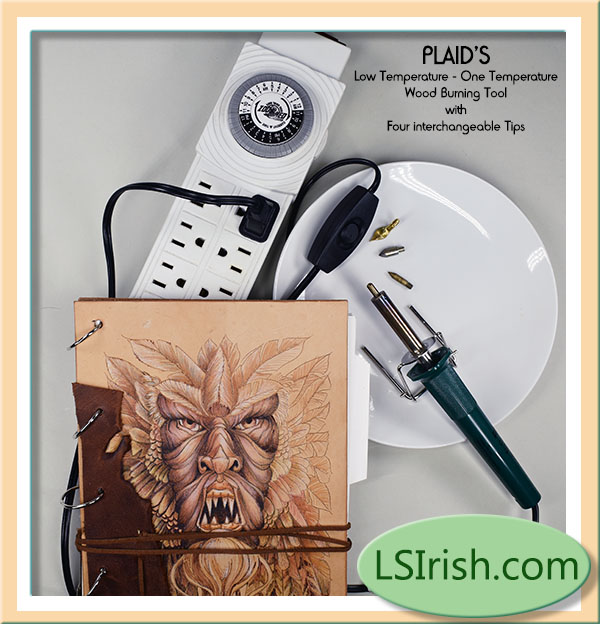
You will need to select a pattern before you can start wood burning. You can choose from simple abstract designs, portraits, and nature-themed artworks. No matter your choice, wood burning is a great way for anyone to express creativity. To begin, you need to learn how to draw. Drawing on a flat surface is a good way to practice freehand. After mastering the art of freehand drawing on wood, you can apply precise wood burning pen strokes.
Wire brush
A practice on plywood will help you learn how to use wire brushes to create wood burning designs. This material is cheap and simple to work with. To avoid toxic fumes, do not burn this material too much or too long. Wood is a great material choice for woodburning projects because it allows for mistakes to be made. A wire brush can be a valuable tool in your wood burning arsenal. A wire brush will give you the flexibility to create various effects.
There are many sizes of wire brushes available. The most common type of wire brush is made from stainless steel bristles. These are great for distressing wood. It is best to purchase a larger wirebrush for large surfaces. Smaller brushes are better for smaller pieces of wood. You can also purchase clamps to hold individual pieces. A wire brush can make wood burning look amazing. You can create beautiful pieces that will be treasured for many years.
Pyrography pen
A pyrography pencil is a tool that lets you burn wood designs using heat. You can easily change the tips to make different designs on different surfaces. Make sure your designs don't burn. Always work in an area with good ventilation. Also, work gloves should be worn when you change the tips. Next, you can start to burn the desired design onto the wooden.
You will need to experiment with different types of wood when you first start out. You'll need to test different pressures and temperatures to determine which one is best for you. To avoid burning holes, it's a good idea practice on several different wood types. If you are starting to write letters, a stencil is a good tool.
Stencil
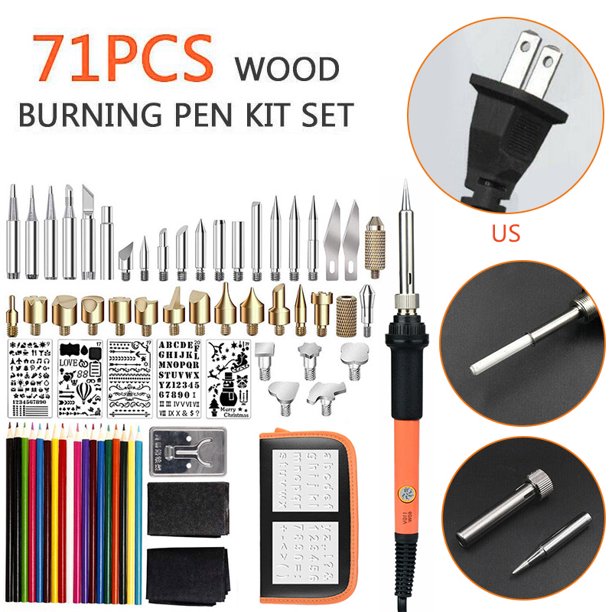
A wood burning stencil is an excellent tool for anyone looking to create a unique design. You can create your own custom design or use a printable stencil. A wood burning stencil is a great way to make lettering easier if you are not an expert. You can also use metal stencils to make wood burning easier. Here are three top wood burning stencils.
A sturdy surface is necessary to cut a stencil made of wood. An X-Acto knife or flexible kitchen mat will work well. It is also a good idea sharpen your knife prior to starting. A larger piece of wood such as a cork trivet will make the stencil more effective. The stencil can also be cut using a ruler and carbon papers. The stencil should hold the weight of the wooden block and be easy to cut.
FAQ
Where can I begin with woodworking
Building furniture is the best way to learn how furniture is made. You'll need tools, and you'll have to make mistakes along the way, but if you keep at it, you'll eventually figure out what you're doing.
You should first choose the project you wish to complete. It could be something as simple as a box or as elaborate as a full-scale entertainment center. Once you've decided on a project, find a local woodworker who specializes in that kind of work. Ask them for suggestions on the tools you will need and where to buy them. You might even ask whether there's someone else you can talk to who does this kind of work.
How do you know which tools are the best for you?
It helps to reflect on your needs and preferences before you shop for tools. Do you prefer metal handles or plastic? What size nails and screws do you usually use? Are you comfortable with power tools, or would you rather use hand tools?
What's the difference between a hobbyist and a professional woodworker?
Hobbyists enjoy making things out of wood, whereas professionals focus more on the quality of their work. Hobbyists tend to take pride and share their creations with family and friends. Professionals will spend hours looking at designs before they start to build a project. Professionals will be meticulous about all aspects of their work, from selecting the right materials to finishing it.
How do you know which type of wood you are working with?
Always verify the label on wood purchases. It should have information about the wood species as well its moisture content and whether any preservatives were used.
Statistics
- Woodworkers on the lower end of that spectrum, the bottom 10% to be exact, make roughly $24,000 a year, while the top 10% makes $108,000. (zippia.com)
- The best-paid 10 percent make $76,000, while the lowest-paid 10 percent make $34,000. (zippia.com)
- Most woodworkers agree that lumber moisture needs to be under 10% for building furniture. (woodandshop.com)
- Average lumber prices rose about 600 percent between April 2020 and May 2021. (familyhandyman.com)
External Links
How To
How to join wood with no nails
Woodworking is a favorite hobby. It is relaxing and enjoyable because you can create something useful with wood. Sometimes you may want to join two pieces together of wood without using nails. This article will demonstrate how to do so to preserve the beauty of your woodwork.
You will first need to trim the edges of your wood pieces before joining them. You don't want any sharp corners to cause problems later. Once you've done this, you're ready to start gluing your boards together.
If you are working on hardwood, you should only use glue on one side. If you are using softwoods such pine or cedar, glue should only be applied to one side. Once the glue has dried, press the boards together until they are fully adhered. After applying the glue, let dry the boards before proceeding to the next stage.
Once you've glued your boards together you will need to drill holes in the joints to accommodate screws. You can choose the type of screw to determine the size of your holes. For example, if you intend to use 1/2-inch wood screws, you need to drill a hole that is at most 3/4 inches deep.
Once you have drilled your holes you will need to drive the screws through each joint and into the backside. Don't hit the board's surface. You could damage the finish. When driving the screws, try to avoid hitting the ends of the screws too much. This will avoid splitting in the wood's ends grain.
You'll need to protect your completed project from the elements. You can seal the furniture pieces or cover the top. It doesn't matter what method you use, you want something that will last many years. There are many options: oil-based varnishes; polyurethane; shellac; lacquer.
You can find these products at most home improvement stores. Just make sure that you buy the right kind for the job. Some finishes are toxic and should not ever be used indoors. So, always wear protective gear when handling them.