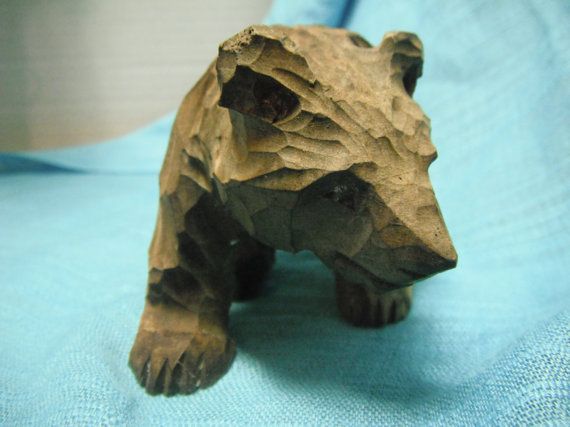
There are many advantages to using a disk sander, from its fast finish to its mitre gauge. While these sanders may not be as portable as some of their competitors, they can deliver the same quality finish. You can find one that best meets your needs, and read on to discover more. Below are some of the most important benefits of a Disk Sander. You have two options when it comes to sanding: one that uses both or one of the methods.
For face sanding, disk sanders can be used
Disk sanders are versatile sanding tools. The rotating disk is supported by an aluminum- or steel backing plate and spins up to sand the material's surface. The disc's center screw and washer are hidden and do not protrude into the work area of the sanded surface. Benchtop disk-sanders are equipped with adjustable worktables to allow for miter slots and end cutting. Disc diameters typically range between 4 and 8 inches. You can get larger models with capacities up to twelve inches.
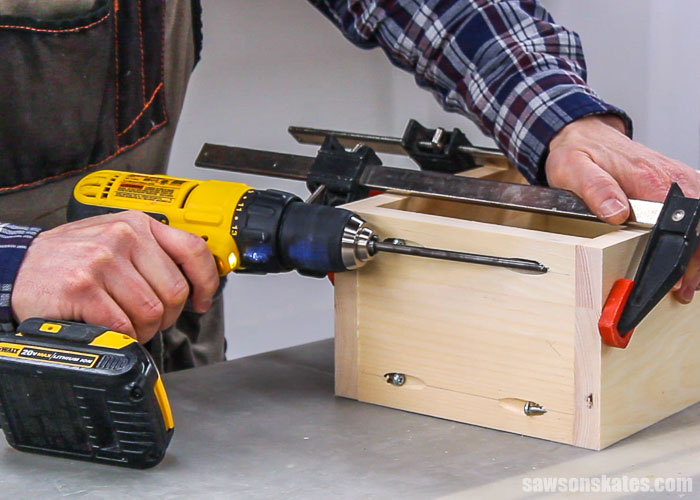
They provide fast finishes
When it comes to speed, disk sanders are an excellent option. There are many sizes of disk sanders, from small hobby machines to large industrial machines. Most home shops use a 12 inch disk. The disks are usually made from pressure sensitive adhesive material. A disc sander can be a great investment if you are working on a project that requires a smooth finish quickly.
They are more compact than other sanders
A disc sander, a hand tool for smoothing small or thin cuts, is a hand tool. They are also less portable than other disc sanders. They aren't as portable but they can be used for various hand jobs like sanding wood, metal and plastic. They are both small- and large-sized and affordable. They can also be used to shape and smoothen various materials.
They have a mitre gauge
A disk sander comes with many benefits, such as a mitre gauge. This features guides the workpiece along the disc, which prevents it from tearing out. Then, it extends the fence height, protecting your fingers from the blade's edge. You can also lock in the miter gauge using a clamp. This tip was provided by Bernard Lewan. Here's how you can set it up.
They come with an adjustable table
Setting the table's height or tilt is the first step to using a disk-sander. A table with an adjustable height should be used. The workpiece must not exceed the table's height. If it doesn't, then the workpiece is too low and could hit the sanding disc. The other controls on your table include the power plant's carriage, quill lock, and table height. If you need more support, you can add a miter gauge extension.
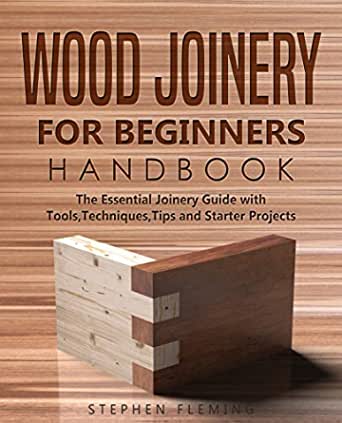
They are equipped with dust ports
A dust collector housing is attached to the disk sander. The entire dust collector housing surrounds and exposes the workpiece. You can expose the entire disc by removing the dust collector housing as well as the front portion. For quick release of bolt 90, a hex wrench34 is provided. To secure the bed 16 vertically, it is necessary to tighten bolt 90.
FAQ
Where can you find free woodworking blueprints?
Woodworking plans can be found online without the need to purchase books or magazines. You only need to Google search. Just enter "free woodworking" into the search bar, and you'll see hundreds of websites where you can download free plans.
How do I learn basic woodworking skills?
A great way to start learning how to build furniture is by building a simple bench for yourself. You can do this project using any type of wood you have on hand at home. You don't need to know which type of wood you should use. Instead, get some pine boards at Lowes or Home Depot. You'll need to sand the bench after it's built. Then, finish it with varnish or a stain.
What is the difference between a hobbyist or a professional woodworker, and how can you tell?
Hobbyists love making things from wood while professionals are more concerned with the quality of their work. Hobbyists tend to take pride and share their creations with family and friends. Professionals will spend hours researching designs and then begin to create a project. They will pay attention to every detail, from selecting the best materials to finishing the project perfectly.
Statistics
- Most woodworkers agree that lumber moisture needs to be under 10% for building furniture. (woodandshop.com)
- Average lumber prices rose about 600 percent between April 2020 and May 2021. (familyhandyman.com)
- Overall employment of woodworkers is projected to grow 8 percent from 2020 to 2030, about as fast as the average for all occupations. (bls.gov)
- The U.S. Bureau of Labor Statistics (BLS) estimates that the number of jobs for woodworkers will decline by 4% between 2019 and 2029. (indeed.com)
External Links
How To
How to join wood without using nails
Woodworking is a favorite hobby. Woodworking can be a fun hobby because you can work with your hands to make useful objects from wood. There are times when two pieces of wood need to be joined together. This article will demonstrate how to do so to preserve the beauty of your woodwork.
Before you can join the wood pieces together, you need to remove any rough edges. You don't want any sharp corners to cause problems later. Once you've done this, you're ready to start gluing your boards together.
When working with hardwood, glue should be applied only to one side. For softwoods like cedar and pine, glue should be applied to both sides. After applying the glue, press the boards firmly until they are completely stuck together. Before you proceed to the next step, be sure to let the glue dry completely.
After you've glued your boards, you'll want to drill holes into the joints where you plan to insert screws. The size of these holes depends on what type of screw you choose to use. For example, if your screw is a 1/2-inch wooden screw, drill a hole that is at minimum 3/4 inches deep.
Once you have drilled your holes you will need to drive the screws through each joint and into the backside. You should be careful not to touch the board's front surface. This could cause damage. Avoid hitting the screws' ends too often when driving screws. This will help prevent splitting of the end grain.
You'll need to protect your completed project from the elements. You can either cover the entire furniture or just the top. You'll want a product that lasts for many years. You can choose from oil-based varnishes or polyurethane, shellac and lacquer as examples.
These products can usually be found at any home improvement store. Just make sure that you buy the right kind for the job. Remember that some finishes can be toxic, so you should not use them indoors. Wear protective gear whenever you are handling them.