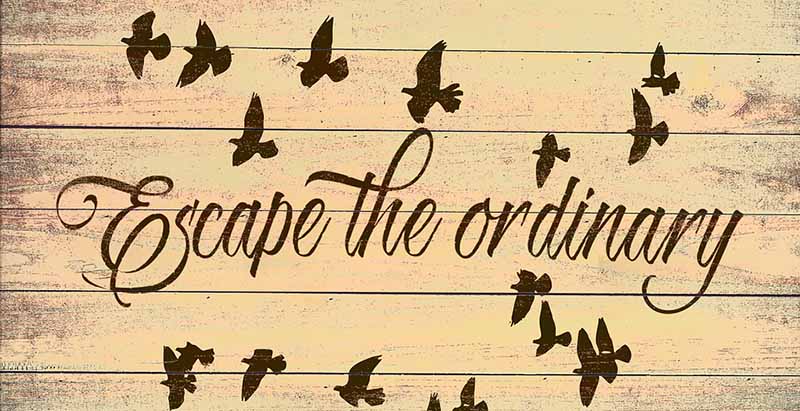
You can make your own carvings by burning into wood, either freehand or with a pyrography tool. A Cricut or laser cutter can be used to create stencils. To make your stencils, you will need a suitable wood burner pen. Here are some guidelines for choosing a suitable pen:
Freehand wood-burning
There are many different materials you can burn in your project, and freehand wood burning is no exception. You can burn most types of raw wood, but staining wood can cause damage. Wood can be used to make ornaments or plaques. You can even make rustic wood signs. You can purchase tools and accessories as well as the basic materials.
Before starting, you should have a piece of wood ready. You can also cut a log and then burn it with a wood-burning device. Once you have the log, you can try your tools on scrapwood to verify their effectiveness. Before burning wood, be sure to test your tools on different shapes, lines patterns, shading, and patterns. It will take a couple of minutes for the tool to heat up, so you shouldn't keep it stationary while burning. When you are satisfied with the object's shape, you can start carving.
Use a Pyrography Tool
A pyrography tool is an easy and effective way of personalizing the appearance of your art. To create unique pieces of art, you can add watercolours and acrylic paint. You should not use pyrography on synthetic materials such as plastic. It can produce toxic gases that can cause harm to the environment and your own health. Additionally, children younger than 12 should not be allowed to burn wood.
When using a pyrography pen, make sure to choose one with a wide range of tips. To get the best results when you're burning wood, it is important to use the tips in succession. The pyrography pen is safe, easy to use, and includes adjustable tips. You can also use it if you have the right knowledge.
Using a laser cutter
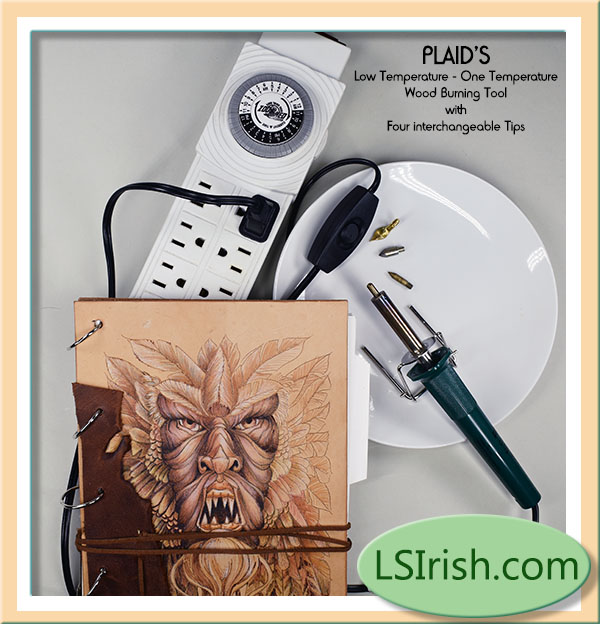
Laser cutting is best for soft and lighter wood because it has less resistance. However, using a laser to cut wood has the downside that it will emit a lot smoke. This can reduce operation visibility and present a risk for health. Maple, bamboo and oak are more difficult woods to burn, due to their complex grain patterns. Lasers can be used on these woods to reduce the contrast of the original surface and new cut edge. This is a great option for veneered timbers.
It is not difficult to burn wood with the laser but it does require extreme precision. If you're not sure how much precision you need, try making some preliminary cuts before finishing a project. This allows you to experiment with the settings so you can determine what type of charring effects your final artwork needs. You can reduce the chance of leaving burn marks by using a slower speed, but it may require multiple passes to cut through the wood.
Using a Cricut machine to create stencils
Cricut is an excellent tool for creating stencils. You can make them from a variety of materials, including vinyl. You can either use vinyl to make a stencil for a single use or use a thin piece of plastic sheet to make reusable stencils. Although plastic sheet stencils do not stick to most surfaces, it is important to use masking tape to hold them in place.
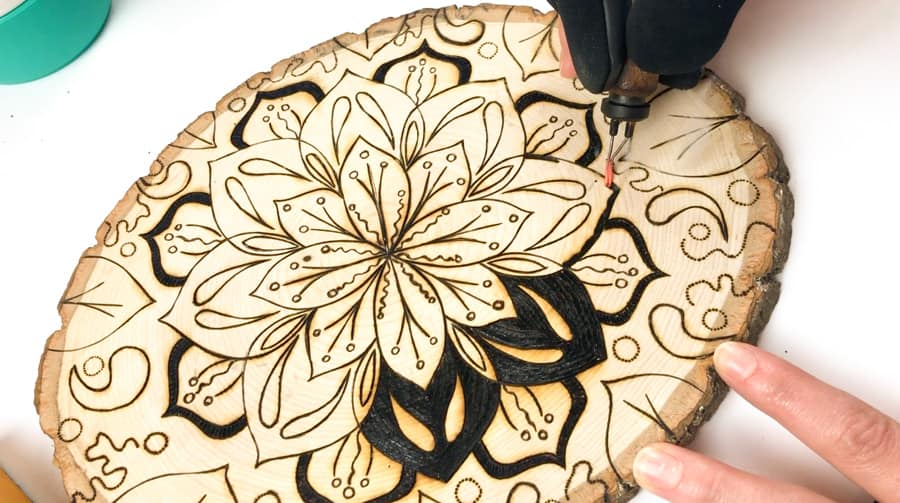
Select a graphic and cut it to create a stencil. It could be a complete design, letters, illustrations, or an entire design. Floating elements, like leaves, can't be cut with the Cricut. These pieces can't be painted so you need to cut them apart. This will allow you to keep the stencil design clear and prevent paint from leaking under it. Once your stencil is in place, you can start painting.
FAQ
What is the difference between a hobbyist or a professional woodworker, and how can you tell?
Hobbyists enjoy making things out of wood, whereas professionals focus more on the quality of their work. Hobbyists tend to take pride and share their creations with family and friends. Before they start working on a project, professionals will spend hours researching the designs. Professionals will be meticulous about all aspects of their work, from selecting the right materials to finishing it.
How can you calculate woodworking pricing?
It is essential to calculate costs as accurately as possible when pricing any project. It is important to ensure that you are getting the best materials prices. Also, consider all other factors that can affect the price of your projects such as skill level, experience, time and cost. Check out our guide on the average cost of common DIY projects to get an idea of how much you can spend on woodwork projects.
How do I know what type of wood I'm dealing with?
Always inspect the label when buying wood. The label should contain information about the wood species, its moisture content, and whether it has been treated with preservatives.
What is the hourly rate for a woodworker?
Hourly rates for professional woodworkers vary depending on many factors such as skill, experience, availability, geographical location, and other variables.
The average hourly rate for a skilled woodworker ranges from $20-$50 an hour.
A woodworker with less experience may be able to charge $10 an hour.
What is the minimum amount I will need to start?
There are no exact numbers because every project is different. These factors will help you get an estimate of how much money is needed.
-
Material costs
-
Tools and equipment
-
Time spent on the project
-
Hourly rate
-
What profit are you expecting to earn?
-
You can hire help, regardless of whether you have a plan.
Start small, if possible. You can make simple boxes or picture frames if you're just getting started. As you gain more experience, you will be able tackle more complicated projects.
Statistics
- The best-paid 10 percent make $76,000, while the lowest-paid 10 percent make $34,000. (zippia.com)
- Average lumber prices rose about 600 percent between April 2020 and May 2021. (familyhandyman.com)
- Most woodworkers agree that lumber moisture needs to be under 10% for building furniture. (woodandshop.com)
- In 2014, there were just over 237,000 jobs for all woodworkers, with other wood product manufacturing employing 23 percent; wood kitchen cabinets and countertop manufacturing employing 21 percent. (theartcareerproject.com)
External Links
How To
How to stain wood
The process of staining wood involves the application of chemicals to the wood's surface, which causes it to change its color. This chemical reaction changes the wood's color from white to brownish. Oak is the most commonly used wood for staining, but other woods can also be stained.
There are many ways to stain wood surfaces. Some methods include mixing the stain along with a solvent like turpentine and then applying the mixture to the wood by brushing or spraying. You can also apply a solution containing water and dye directly to the wooden surface. The stain can be mixed with paints and varnishes to become part of the final coating.
Preparing the wood surface is the first step to staining it. Cleaning the wood thoroughly removes any dirt or grease that could interfere with applying the stain. Sanding smoothens any scratches or rough spots. The next step is to choose the stain type you want. There are two types of stains that can be used: penetrating and non-penetrating. Penetrating stains penetrate deeper than non-penetrating stains, which makes them great for dark colors like mahogany. Penetrating stains are best paired with lighter colors, such as maple.
You will need to decide on the type of stain you want to use, and then prepare your tools. Paintbrushes are great for applying stain because they allow you to evenly spread the liquid across the surface. A few rags are also handy to clean up any spillages after you have finished painting. If you plan on mixing the stain yourself make sure that you have enough containers to hold the different components.
Once you have prepared your materials, start by cleaning the area where you plan to stain the wood. Use warm water and soap to clean away dirt and dust. You can wipe down the entire furniture using a damp rag with clean water. If you intend to stain darker wood, make sure you get rid of any debris.
Apply the stain. Next, apply the stain to the furniture by starting at one end. You should work slowly and carefully. Continue moving along the grain until you reach your opposite end. Keep the stain from dripping off the wood's surface. Allow the stain to dry completely before you move on to the next step.
Protect the painted surface with a coat polyurethane paint sealant. Three coats of polyurethane sealing agent are required. Allow the third coat of polyurethane sealer to dry overnight before applying the final coat.