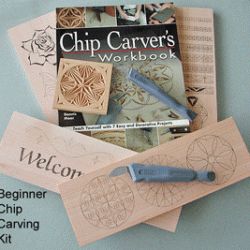
There are many methods to carve a Gnome. Before you begin carving, here are some key points to keep in mind. This project is both fun and rewarding, in addition to the actual carving. It involves multiple layers and can be a great way of learning how to carve the gnome. There are many creative ways to enhance your gnome carving. These are just three tips for carving a wood gnome.
Freehand carving a gromme
These tips will help you succeed when carving a gnome freehand for Christmas ornaments. It is possible to carve the gnome without a knife. A micro V-tool will be necessary if you wish to add fine details to your hat rim. Fortunately, a gnome is a fairly simple carving project, and you can even carve a gnome in your spare time!
A gnome is an excellent way to demonstrate your skills in freehand carving. They were once popular garden ornaments. Making a gnome out of wood is a great exercise in skill. It will help you gauge how skilled you are and where you need to work on your craft. You can also use it as a measuring stick to determine design, depth, detail, or design. After mastering the drawing of the gnome, you can start sculpting his features.
Whistle carving is a great project for any woodcarver.
The whistle is an excellent project for woodcarvers. A simple, but functional object, the whistle can be fun to carve. To make your whistle a useful piece, you need to know the steps. We will be covering the entire process of carving a whistle, starting from preparation until the final product.
To begin, you will need to have a straight-edged cutting knife and some non-toxic oils. Although carving a wooden gnome can seem daunting, this is a very simple project that will improve your woodcarving abilities and provide a great outlet for creativity. It's also one of the best beginner projects, as it will provide you with an opportunity to practice many woodcarving techniques.
Adding creativity to gnome carvings
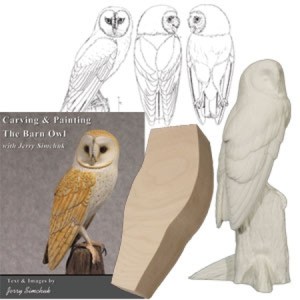
Adding creativity to gnome carvings can be as simple as adding a colorful hat. A wood-carved gnome may be a whimsical decoration, or a sneering troll might make your heart melt. Gnomes are an excellent way to add personality to your garden, and this can be done with various materials, such as wood, stone, and stone.
How to make a gnome with wood
First, measure the wood block you are using to carve a gnome from wood. You will then draw the gnome's anatomy including the head, body, feet and belt. To create smooth corners for the face, you will need to make V-cuts in particular areas. With a chisel/knife, cut V-cuts where needed. You will then need to cut a piece approximately 1.5mm thick with a microV-tool. This will give you an elegant curved edge to finish your beard and hat.
It is easy to carve a gnome. This is because there is so much potential to produce high-quality work. If you carve a gnome each week, you will see improvement in each stage. While this may not happen with every project, weekly carving progress will allow you to make noticeable improvements in design, shape, and facial features.
Add a new gnome to your world of gnomes
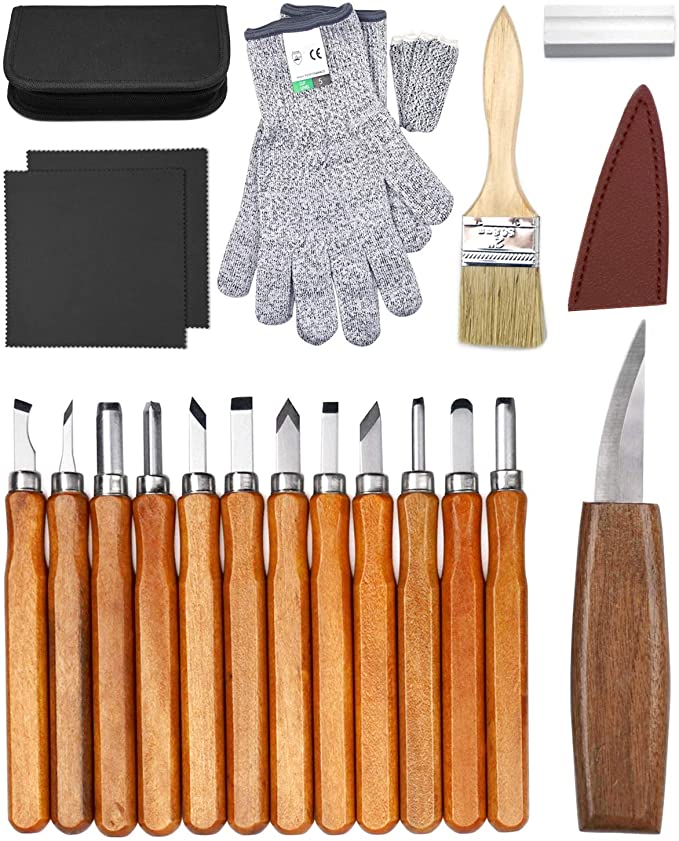
The Gnomes of the Underdark and other RPGs usually have one recurring character: David. This character isn’t insane. He has traits like Speak Fluent Animal, Can't Argue with Elves, and Telepathy. He has the ability to put up road signs and throw people off. David and Lisa could even have a rivalry.
Gnomes can be powerful casters but are also adept at reading arcana. In addition to this, they're the only playable race in the game. Other gnomes, like undead and leper gnomes, share the same skeleton animation. Gnomes have always had a strong presence in Kirin Tor. Their founding member Meryl Felstorm had a gnome as an associate of his.
FAQ
How can a beginning woodworker make a living?
Many people want to open an online furniture business and are learning how to build it. But if you're just getting started building furniture, there are other ways to earn money besides selling on Etsy. You could sell at craft fairs or local events. Offering workshops could be another option for those who are interested in learning how to build their furniture. If you have the experience to be a carpenter, builder, or a designer, you may consider offering your services in remodeling homes or creating custom pieces.
What kind of wood should you use?
Oak, maple, cherry and mahogany are the most common wood types used for woodworking. Each type of wood has its own unique characteristics that can affect the final product's appearance. For example, oak tends to be darker and harder than other woods. Birch, which is lighter and soft, is more heavy than mahogany. There are two options: solid wood and veneers. Veneers are thin sheets or wood that are glued together into one layer.
Do you have any other information I should know about woodworking and/or the process of making it?
It's easy to underestimate the amount of work involved in making furniture. The hardest part of the process is actually finding the right wood. There are so many varieties of wood available that choosing one can be difficult.
Another problem is that not all wood has uniform properties. Woods can warp, split, or crack over time. Before purchasing wood, you should consider these factors.
Statistics
- Average lumber prices rose about 600 percent between April 2020 and May 2021. (familyhandyman.com)
- Overall employment of woodworkers is projected to grow 8 percent from 2020 to 2030, about as fast as the average for all occupations. (bls.gov)
- In 2014, there were just over 237,000 jobs for all woodworkers, with other wood product manufacturing employing 23 percent; wood kitchen cabinets and countertop manufacturing employing 21 percent. (theartcareerproject.com)
- If your lumber isn't as dry as you would like when you purchase it (over 22% in Glen Huey's opinion…probably over 10-15% in my opinion), then it's a good idea to let it acclimate to your workshop for a couple of weeks. (woodandshop.com)
External Links
How To
How to stain wood
Stain wood is a process that involves applying chemicals to the surface of wood, which changes its color. This chemical reaction causes the wood to change from white to brownish red. Oak is the most common wood type for staining. However, you can also use other wood types.
There are many ways to stain wood surfaces. Some methods include mixing the stain along with a solvent like turpentine and then applying the mixture to the wood by brushing or spraying. Other methods use a solution of water and dye applied directly to the wood. It is possible to mix stain into varnishes and paints, making it part of the finishing coat.
The first step in staining wood is preparing the surface. Cleaning the wood thoroughly removes any dirt or grease that could interfere with applying the stain. Sanding smoothens any scratches or rough spots. Then you must decide what kind of stain you want to use. Penetrating stains are different from non-penetrating. Penetrating and non-penetrating wood stains penetrate deeper than other types, making them perfect for dark colors like mahogany. Non-penetrating oils work best when used with light colors, like maple.
After choosing the type and application method you prefer, gather your tools. The best tool for applying stains is a paintbrush. It allows you to evenly distribute the liquid over the surface. You should also have some handy rags to wipe up excess stains after you finish painting. If you plan on mixing the stain yourself make sure that you have enough containers to hold the different components.
After you have prepared the materials, you can clean the area where you want to stain the wood. To remove dirt and dust, use warm water and soap. Wipe the entire piece of furniture with a rag dampened with clean water. You should remove any debris, especially if your plan is to stain darker wood.
Next, apply the stain. Start at one end of the piece of furniture and brush or spray the stain onto the wood. You should work slowly and carefully. Continue moving along the grain until you reach your opposite end. Be careful not to let the stain drip off the wood's edge. Before moving on to the next steps, allow the stain drying completely.
Clear polyurethane is used to protect the painted surfaces. Three coats are recommended for polyurethane. Allow the third coat of polyurethane sealer to dry overnight before applying the final coat.